How The V2 Came to Be

Words by Steve Maier, Designer of the NoLimitz V2
NoLimitz foil masts started as a result of a lack of quality masts being offered to the market. It wasn’t a situation of entering the market with a plan to make a bunch of money, it was strictly because most of the masts on the market were absolute crap. They were heavy, they weren’t stiff enough, they twisted around like a wet noodle, and they weren’t very efficient. None of that worked for me as the masts were negatively impacting my experience learning how to foil –their unpredictability resulted in crashes. If most of the brands had been making good masts at that time, NoLimitz foil masts would not exist today.
The industry has grown a huge amount in the past couple years. Companies are paying attention to the mast as the critical part of the overall system that it really is. They have been chasing NoLimitz to make a mast that competes, and I am very happy about this as it improves the quality of gear available to everyone.
The NoLimitz V1 mast has gone through many iterations since its first release. The V1 mast we ship today is very different from what we were selling a year ago. We made a lot of mistakes along the way with the V1 mast. Those mistakes allowed us to learn a lot about what does and does not work in the real world, which frequently was much different than expected. Adhesives that are tried and true for highly loaded rockets failed on foil masts. Paints that were presented as “bulletproof” caused issues with ventilation and failed over time in a saltwater environment. Metal finishes that were developed for corrosive applications did not hold up long term, at least not to our expectations. And don’t get me started on the constant chase of ensuring our masts fit properly with every fuselage interface which seems to change nearly monthly with some brands.
As I developed NoLimitz V2 mast, I listened to the feedback we got from riders in all disciplines all over the world - what they like, what they don’t like, what they would like to see better, etc. From this feedback, my focus was on taking things to the next level in terms of performance and durability. The durability part was pretty straight forward as we had a lot of tough lessons over the past couple years that taught us what does and does not work in the real world. You will notice our metal fittings have changed color, that is not for cosmetics but driven by function. The black anodize is significantly more durable than the previous blue. As a rider, I want the best possible riding mast and I want it to be durable.
The performance wish list when I started design on V2 was:
Elimination of Ventilation (no one likes to randomly eat it, especially when in a critical section or going fast)
Efficiency of the foil section – I wanted a faster, low drag section that has great glide.
Increased bending stiffness. V1 is a little soft on flex for bigger guys (me) when pumping
Optimize strength to weight ratio of mast (keep it at light as possible while meeting worst case loads)
It has been a long time since I had aero in college and there are a lot of way smarter folks in the world that have been designing hydrodynamic systems for decades. Based on these two simple facts, I started to study both aerodynamics and hydrodynamics and talk to a lot of really smart hydro folks. This resulted in more questions than answers, but the one thing that became very clear to me was that I needed to really define what we wanted to accomplish and figure out how to quantify the options.
Not surprisingly, the Department of Navy has a lot of research on surface piercing struts dating back to the 50’s. I started reading every report I could find (this is great bedtime material if you suffer from insomnia). After a few months of reading thousands of pages, I found a lot of good data that correlated to what we needed for our sport. With this newfound knowledge, I started calling up contacts within the Americas Cup world and getting their advice. ICE has been working with Americas Cup teams for decades building various carbon fiber parts for their amazing sailboats.
I gathered up all my notes and started in with the serious calculations. I evaluated hundreds of airfoil sections across the speed range in which we operate, factoring in key factors like drag, critical angle of attack and lift. This led to ever growing spreadsheets filled with data. From this, I was able to narrow my focus to a handful of airfoil sections that looked promising. I asked myself, which one is best for our purpose and how can I modify these to make them better? During this process, I was balancing the search for the “perfect section” with the reality of it needing to be structurally able to meet the strength and stiffness criteria I had outlined.
At this point in the design process, it became clear I needed to be running these sections though Computational Fluid Dynamics (CFD) to get a higher degree of confidence what would work best for V2. I did some checking into having the CFD work done for me and just about fell over from the quotes so it was time to learn CFD. It wasn’t as bad as I had expected; I was able to play in the shallow end of the CFD pool and get the data I needed. This new tool became a little addictive, I quickly settled on one airfoil section then started tweaking it to see how it could be improved. It was amazing to see how making changes of a few thousands of an inch impacted the results, and I was able to quickly settle on the compromise foil section that would become the V2.
Oh, I guess I haven’t brought up that “compromise” word before, sorry. Everything with the design of a foil or a foil mast is a series of compromises. You give away a little efficiency here for more resistance to ventilation there. You make it thicker for increased stiffness, so the foil tracks where you want it to instead of it wandering off on its own.
Once I had a foil section I was going to run with, it was time to finalize the actual mast’s structural design. We knew our baseline bending and twisting stiffness for V1 so that is where we started. I wanted the V2 to maintain about the same chord length because the V1 turns well, and increasing chord would impact turnability (I mainly chase waves so turnability is important to me).
For a given chord length and foil section, you end up with a thickness,. You really cannot change that without changing the actual section itself. Based on keeping the chord very close to V1, I came up with a thickness of 15.5mm. This thickness with the improved foil section would meet the goals of improved efficiency. Now, some folks on the internet talk about chord having a bigger impact on drag than thickness and that is simply not true.
A simple way to think about this, please try to stick with me here, is try to push something wider than something else through the water. The wider it is, the harder it is to push through the water as you have a huge increase in drag. Stick your hand out the car window – what has more force pushing on you, one finger out or three? Now, if you take two items the same thickness with one being twice as long as the other and push them through the water, the longer one will take very little more force to push along…Nowhere near the drag increase you see with making something thicker.
The formula for Force due to Drag has cross sectional area (thickness) as one of its largest drivers. The Coefficient of Drag (Cd) will be affected by the chord length, but Cd itself is a very small number compared to cross sectional area.
Once I had the foil, thickness, and chord length figured out, it was time to make up the first protypes and get them into testing. I put a slight taper into the mast from board to fuselage to distribute the mast bend lower along the mast. This helps with dampening some of the foil movements that occur.
We machined new tooling for NoLimitz V2 and had the first test masts on the water in July of ’22. The initial feedback was fantastic- we could not get it to ventilate, the mast was a lot faster, and it had great glide. The foil section was a winner. Then, we had to really dial in the stiffness and that took a lot more testing and data gathering. All along, we had assumed the loads on the mast from being ridden based on some rough calculations of how heavy a rider was and how many G’s could be imparted on a mast while riding. But, we needed real data to dial in our design so, we decided to instrument a mast and put it on the water.
The first gizmo mast was kind of crude with a big electronics box strapped on the deck of a board hooked up to wires running through the mast. We got some good data from this set up but realized we needed a “cleaner” test mast to get better data from more sources (including surfers who rail some of the hardest turns of any discipline). That led to developing the 2nd iteration of an instrumented mast, a much cleaner version with the the electronics recessed inside the board, which we gave to top riders and told them to try to break it. Well, they never broke the mast but we had lots of issues getting good data as they did break foils and twist fuselages. We managed to get some data on peak loads just before these other components failed, so we had numbers to keep working with for the V2.
V2 testing continued through winter of ’22-’23 with many iterations of mast stiffness. We also started more extensive testing of other brands masts to verify their bending stiffness, as it is far too subjective just pushing on a set up on the beach or riding it. As we suspected, the Axis 19mm Aluminum mast was (and still is) the stiffest mast in bending on the market. This is one reason why folks that pump a lot love that mast, no wasted energy in the pump but, they hate the drag of the thick section.
We made stiffer and stiffer versions of the V2, at times trading off torsional stiffness for more bending stiffness. Torsional stiffness is very important for a foil mast and is overlooked by the industry. If the mast twists around like a wet noodle, the foil is going to wander where it wants to, not where you want it to go. This leads to going into a turn and waiting for the foil to finally catch up with you – which usually happens with a pop which is unsettling and is the last thing you want during a bottom turn into the pit of a big wave. That’s why NoLimitz focuses as much on the torsional stiffness of our masts as the bending stiffness, to ensure the foil always tracks where you are telling it to.
On the bending side, the really stiff mast rode so direct that it took a while to get used to. Any little input was immediate and any disturbance of the foil was magnified. It felt like you were on edge all the time which, at first was not a comfortable feeling but after a session, a little addictive as you learned to trust it. You could push as hard as you wanted to and it would not fail you, it would just respond immediately. Testers loved the glide and one tester made several tacks in a row for the first time they had ever made a tack. He contributed it to the added glide and his confidence from the mast.
This is how we got to the NoLimitz V2. It is an all-new mast from top to bottom, not just a new foil section or some graphics changes. It is thinner, faster and stiffer than our original. It does not ventilate. We have changed to forgings for our board fitting to increase stiffness and strength. Fittings have a new coating that is much harder and more corrosion resistant than anything we have tried in the past. The interface between the fittings and carbon masts have been redesigned to improve load transfer and bond performance. Fiberglass has been added at all carbon to aluminum interfaces to minimize galvanic corrosion.
The NoLimitz V2 once again elevates the target for the rest of the industry. We are not going to leave well enough alone.
Now, this may all sound like a hell of a lot of work to get V2 out to the world and it was. I enjoyed the hell out of it as I love a challenge and I love learning new things. I’m not just sitting behind a computer doing this, I am on the water riding and testing all that I can. I’m frequently in the shop with a grinder making tweaks to see how it responds. I’m not a shredder, I’m too damn old for that, but I still put myself in harms way more often than I should in the waves and I must trust that my gear is not going to let me down.
We will continue to improve upon our designs especially as this sport continues to develop. You can find me on the waters of the North Shore of Maui all winter long and in the gorge in the summer. I have the utmost respect for others in this industry that are out on the water all the time testing and developing their products, folks like Alex Aguera, Ken Winner and Dave Kalama to name a few, who are on the water constantly testing and innovating new ideas. We all win from the passion and dedication of these great watermen.
Steven Maier
President/CEO
Innovative Composite Engineering / NoLimitz
Foiling in the picture below at Ka’a
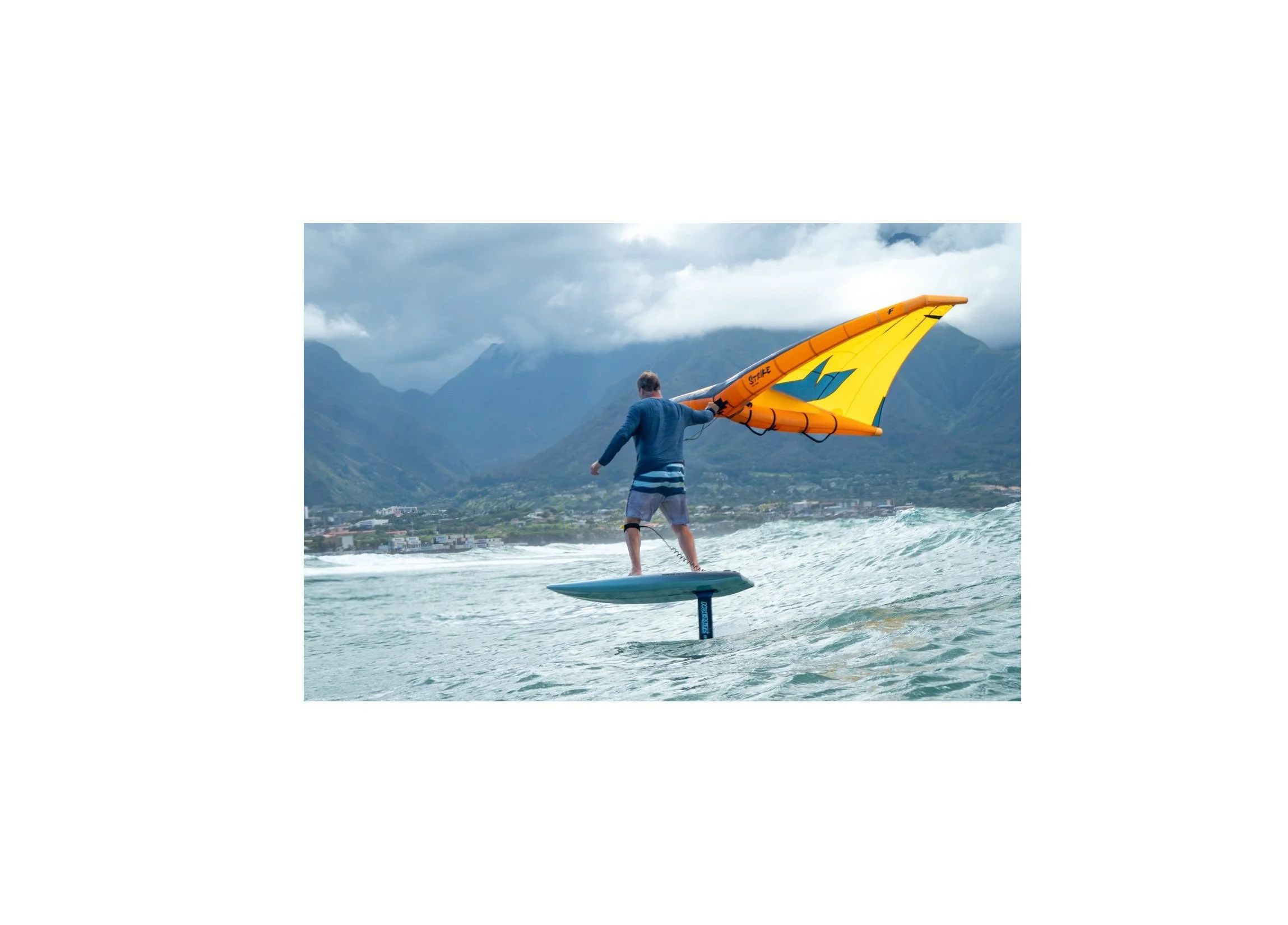